Introducation
Polyurethane is the world of material, proportion, and property. Most of these systems contain Isocyanate and Polyol which reacts and create Urethane groups in the polymer backbone.
The components in PU systems vary with application and there is a lot of books and article about them that I don’t think it is necessary to mention.
Isocyanate:
- Aliphatic: HDI, IPDI (Higher Price, Decorative Application)
- Aromatic: pMDI, TDI (Lower Price, Bulk Application)
Polyol:
- Polyester
- Polyether
Catalyst:
- Foaming: DABCO
- Gelling: DBTDL
Filler:
- CaCO3
- Talc
- SiO2
- Fumed Silica
Blowing agent (for foam)
- Physical: Pentane
- Chemical: Water
Other additives:
- Pigment
- Flame Retarder
- Solvent
The ratio of NCO/OH plays an important role in PU systems.
Foam:
The reaction of the free Isocyanate group with water can produce CO2 in the polyurethane matrix and make foam. Therefore, the NCO/OH must be higher than 1 in order to produce free NCO. This ratio controls the proportion of 2 parts in 2K systems or during pre-polymerization in 1K systems. In this project, we use domestic Isocyanates and some polyether and Castor Oil with other additives to make foams for injection in cracks which can be used in construction and repair projects.
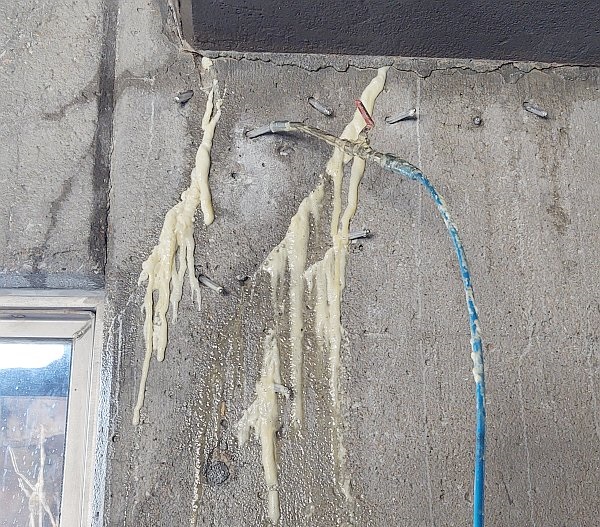
Flexible Foams:
The reaction condition of NCO with OH is easy and can easily done in the laboratory. Therefore, the soft segments of polyurethane (which creates softness) can be increased in polyol with pre-polymerization. Furthermore, the NCO/OH less than 1 is a good option for creating polyol which can be used for soft foams.
Sealant:
In this system, the reaction of NCO and OH needs to be complete (NCO/OH close to 1). Additional OH makes surface tack meanwhile, additional NCO can create a glassy bubbly surface. (Reaction of moisture with NCO and polyurea as a result of produced amine). We use domestic materials for sealant and rheological controlling additives.
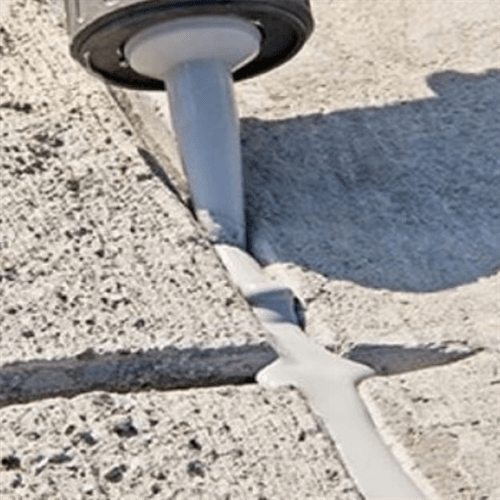